Service and support
Maximize long-term profitability
With Alfa Laval as your service partner you ensure maximum return on investment over the lifetime of your heat exchanger. We offer a wide range of services that keeps your heat exchanger operating with high efficiency and low operating costs:
- Regular and preventive maintenance
- Reconditioning
- Audits and inspections
- Emergency assistance
- Upgrades
- Installation and commissioning
- Spare parts and custom tools
- Training
Ready to help
Our global network of service technicians is on stand-by to assist you on site at short notice in case of emergencies. Within a few days we will have personnel on your site ready to help you repair or inspect your heat exchanger, regardless of type or manufacturer.
We know the importance of keeping service stops short and we always plan and perform our service work in the shortest possible time to minimize downtime.
Service agreement
You can also enter into a service agreement with us, giving you full peace of mind and predictable maintenance costs.
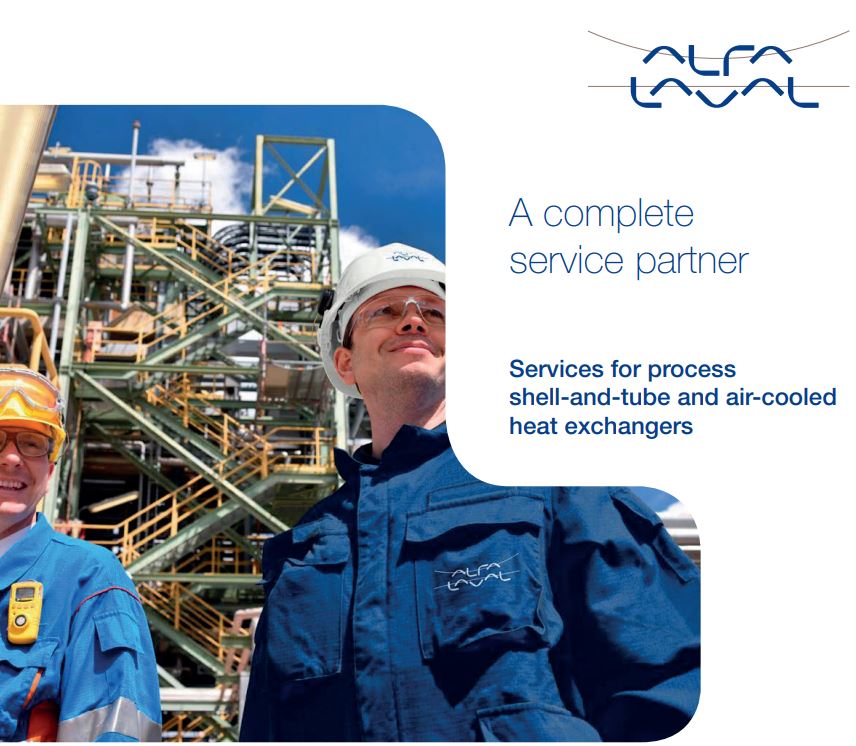
A complete service partner
With Alfa Laval as your partner you have full support from our experienced service teams around the world.
Contact our service team
Please send as much information as possible regarding your service requests, so that we can help you as soon as possible.
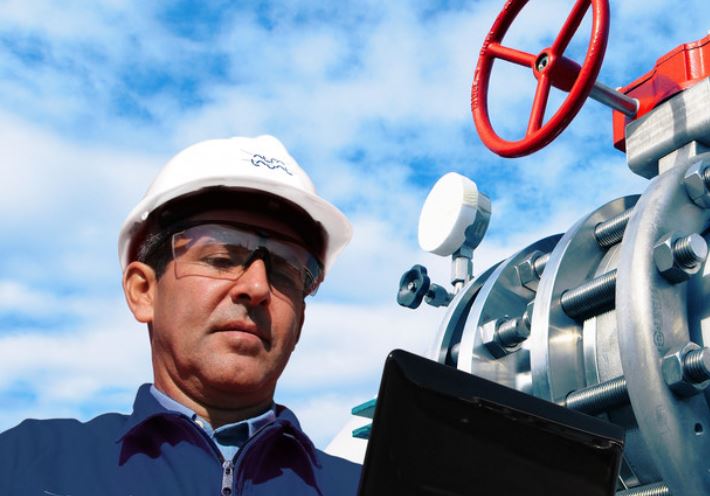
After sales engineering
When you need to upgrade existing equipment, our mechanical and thermal engineers can help you analyse the condition of your heat exchanger and propose how you can improve performance and/or prolong its lifetime.
Key services
- FFS (fitness for service)
- FEA (finite element analysis)
- Non-linear stress analysis
- Thermal re-rating (or upgrade)
Repair intervention
In case of emergencies, our service technicians are available 24/7 and ready to intervene on your heat exchanger, regardless of type or manufacturer. Our staff is safety trained and ready to reach you worldwide within 72 hours from your call to give our customers the best possible assistance.
Our team
- Our personnel is selected for customized intervention.
- Qualified ASME level III personnel is available for any type of your heat exchanger.
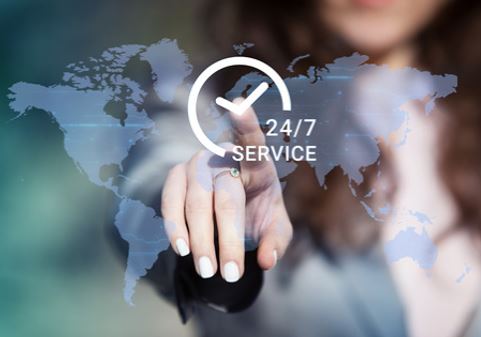
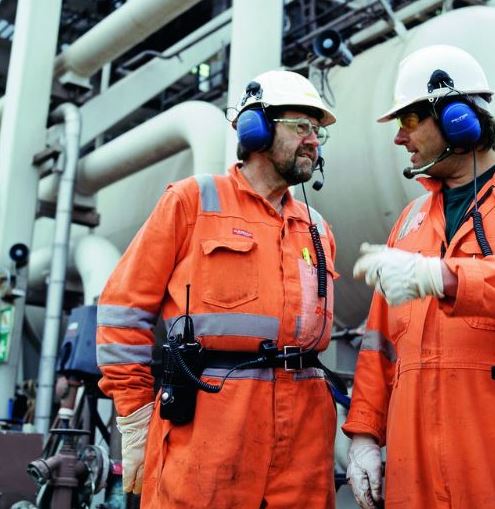
Maintenance site project
We know how important maintenance is for our customers. We take care of your equipment on site providing solutions to improve efficiency and lifetime.
Maintenance site
- Large projects
- Standard projects
- Audit / inspection projects
Inspection audits
Tube-to-tubesheet joint radiographic inspection allows combined benefits on execution time, higher safety, higher quality.
Inspections
- We offer EC, RTF and IRIS inspections, including the development of customized probes.
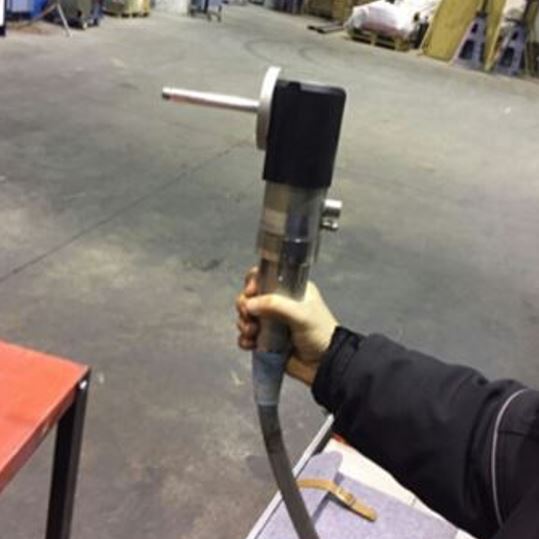
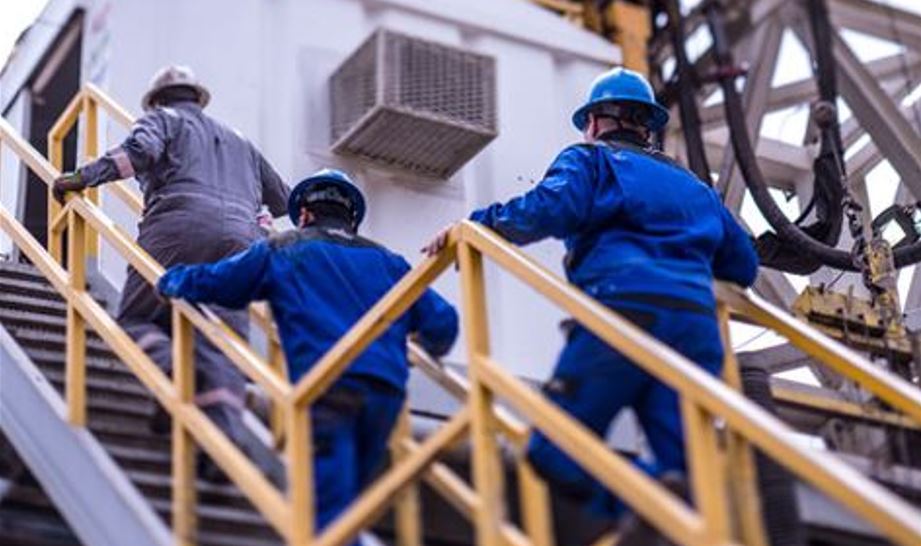
Replacement
For our customer, achieving the right schedule, by guaranteeing a high quality, is a key. This is our commitment. Smart service means reliable solutions for any type of replacement.
Spare parts and customized tools
We can provide all necessary spare parts, from single components such as bolts and gaskets to pre-assembled units like valves and tube bundles. We can provide tools that are custom designed for your equipment to facilitate work on site.
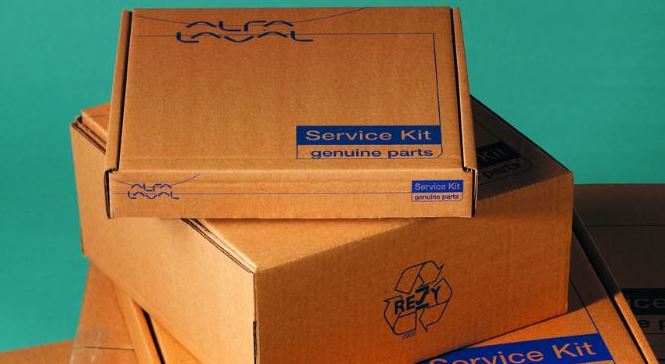